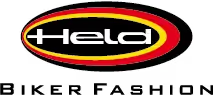
Held Biker Fashion: Materiallogistik sorgt für hohe Liefertreue
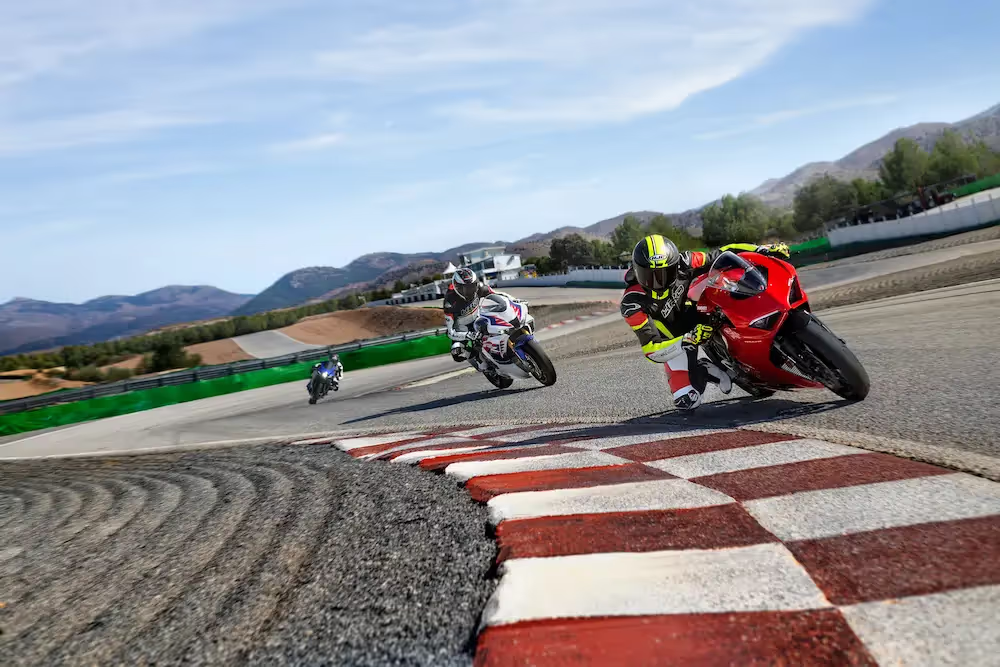
Die Held GmbH mit Hauptsitz in Burgberg im Allgäu ist ein Familienunternehmen in dritter Generation. 130 Mitarbeiter sowie mehr als 3.000 Händler in Europa stehen für den Erfolg des Unternehmens. Die Held GmbH hat sich im Bereich Motorsport vom Motorradhandschuh-Hersteller zu einem erfolgreichen Vollsortimenter für Motorradbekleidung entwickelt. Bei den Leserwahlen der Zeitschrift „Motorrad“ wurde Held 2023 etwa zur „Best Brand“ in den Kategorien Handschuhe, Textilkleidung und Bikerjeans gewählt. Arbeitsschutzbekleidung zählt seit vielen Jahren ebenfalls zum Produktportfolio. Sie wird seit 2023 unter der Marke „Held Work Protection“ vertrieben und stellt ein weiteres Standbein des Unternehmens dar.
Das Allgäuer Familienunternehmen Held GmbH zählt zu den Marktführern für Motorradbekleidung im deutschsprachigen Raum. Neben einer kleineren Produktion am Firmensitz, wird ein größerer Teil des Sortiments in spezialisierten und zertifizierten Fertigungsunternehmen weltweit, produziert. Entsprechend anspruchsvoll ist die Materiallogistik. Der langjährige Anwender des ERP-Systems DIAMOD hat deshalb das Modul Materiallogistik in Kombination mit Scannern und Tablets eingeführt. Seitdem profitiert Held von einer hohen Prozess- und Bestandssicherheit im Materiallager sowie einer sehr hohen Liefertreue.
Die Held GmbH arbeitet bereits seit mehr als 25 Jahren mit dem ERP-System DIAMOD des Karlsruher Branchenspezialisten texdata. Bestellungen des Fachhandels wie auch aus dem Webshop werden mit dem Lagerverwaltungssystem DIALOG schnell und sicher abgewickelt. Doch auch die Versorgung der spezialisierten Lohnfertigungsunternehmen mit hochwertigen Rohstoffen wie Leder, Textilien oder High-End-Membranmaterialien wie etwa Gore-Tex ist anspruchsvoll. Von Portugal über Ungarn, bis in den Fernen Osten, arbeitet Held mit zertifizierten Spezialbetrieben zusammen, welche die hohe Qualität der Produkte gewährleisten.
Diese Unternehmen werden vom Unternehmenssitz in Burgberg aus mit der benötigten Rohware versorgt. Diese Materiallogistik konnte lange Zeit mit einfachen Hilfsmitteln wie Excel-Tabellen bewältigt werden. Mit zunehmender Komplexität der Prozesse erwies sich der unzureichende Überblick über den jeweils aktuellen Lagerbestand jedoch als Manko und es kam zu erheblichen Rückständen bei der Belieferung der Produzenten. Der Geschäftsführung war deshalb schnell klar, dass eine leistungsfähigere Lösung gebraucht wurde.
Sichere Prozesse mit Scanner und Tablet
„Da unser Berater von texdata unser Unternehmen sehr gut kennt und wir seit Jahren vertrauensvoll zusammenarbeiten, haben wir zunächst das Gespräch mit ihm gesucht“, berichtet Gerhard Kuhn, Leiter IT und Web bei der Held GmbH.
Anschließend sei die Entscheidung zur Einführung des Moduls Materiallogistik und zur Optimierung des Workflows im Lager gefallen. Neben der Softwarelösung war die Einführung von per WLAN angebundenen Windows-Tablets und Bluetooth-Scannern der Schlüssel dazu, sichere Prozesse im Lager zu etablieren. Im Wareneingang findet heute die Erfassung per Scanner, die Qualitätskontrolle und anschließend die Einlagerung der Ware statt. Bei der Kommissionierung der Ware verwenden die Lagermitarbeiter Rollwägen, an denen Tablets fixiert sind. Mit leichten Bluetooth-Scannern erfassen sie Lagerplätze und Ware per Barcode und übermitteln die Daten via Tablet in das ERP-System. So ist der Warenbestand immer aktuell.
Bestandssicherheit auch bei zu konfektionierender Rohware
Zu den Besonderheiten des Materiallagers gehört es, dass viele Materialien bei Held nicht nur kommissioniert, sondern auch auftragsbezogen am Lagerplatz konfektioniert werden. Beispielsweise schneidet ein Mitarbeiter eine bestimmte Menge Kevlar-Jeansstoff von einer Rolle. Das System druckt dann direkt zwei neue Barcode-Labels aus. Eines, welches die Information über die gekürzte Länge der Rolle, welche am Lagerplatz verbleibt, enthält und ein weiteres mit der Länge der entnommenen Materialmenge, welches später am Packplatz gescannt wird.
Während im Fertigwarenlager in Kempten täglich große Mengen von Sendungen via Paketdienstleister an Händler und Kunden verschickt werden, sind es im Materiallager oft Paletten und Container, welche via Spedition zu den Fertigungsbetrieben in aller Welt auf den Weg gebracht werden.
Aufgrund der guten Zusammenarbeit zwischen Softwarehaus und Anwenderunternehmen und des großen Engagements im Projektteam verlief das Logistikprojekt sehr gut. Während der Umstellung auf die neuen Prozesse in der Materiallogistik war das Unternehmen durchgehend lieferfähig.
Nach mehr als einem Jahr im Betrieb hat sich die neue Lösung bereits bewährt: Lieferrückstände gehören der Vergangenheit an. Alle Sendungen erreichen die Fertigungsbetriebe zu den vereinbarten Terminen. Die Bestandssicherheit im Lager hat sich signifikant erhöht. Die Einführung des DIAMOD Moduls Materiallogistik in Kombination mit Barcodescannern und Tablets hat für Transparenz und Prozesssicherheit gesorgt.